Are requests fulfilled on time when your employees need to ask for materials or services to do their jobs? Or do they find themselves waiting around for what they need as the approval process drags out to get them the funds they need to order supplies?
Do some of your suppliers cause delays for your company in getting what you or your employees need to complete your projects?
When delays happen, profits decrease, and customers lose trust in your business.
If you have issues with your processes, consider using a SIPOC, a tool that helps visually dissect a process into its key components.
In this article, we will cover:
- What is a SIPOC?
- What is the difference between a process map and a SIPOC diagram?
- Creating a SIPOC diagram
- What are the benefits of a SIPOC diagram?
What is a SIPOC?
A SIPOC is a diagram used in Six Sigma to show the suppliers, inputs, processes, outputs, and customers in a business process. The diagram is a high-level overview to inform decision-makers about your processes.
A SIPOC is used in Six Sigma to define, measure, analyze, improve, and control (DMAIC) during the define phase.
The six elements of a SIPOC
The SIPOC is made up of six elements, which are:
Process name
The diagram should include the name of the process you are documenting. Example processes could be an online ordering system or the process to serve customers at a restaurant.
Suppliers
Suppliers are whoever provides the inputs (such as materials) needed to create your product or service.
Supplier examples include stores where you purchase supplies, an IT department that creates software your team uses, or a manufacturing company that makes the machine parts for your production line.
Inputs
Inputs are what you use to make your product or service.
For example, a restaurant would use customer orders (in-person orders, phone orders, internet orders from their webpage, or orders made through the company's app), raw materials (ingredients), ovens, and things like measuring cups, bowls, and pans as inputs to make the product (food).
Processes
Processes are the steps your inputs go through to make a product.
In a SIPOC, this is usually only a high-level outline of the process. A process map goes into more detail, but we'll cover that in a bit.
For example, the process steps in a recipe would be the making of a dish. A restaurant would have a process for serving their customers. It'd begin with seating them when they arrive (or receiving the order through the website, a phone call, or an app) to delivering the food.
Outputs
Outputs are the products or services created as the results of your processes.
A restaurant would have an output of food and drinks. One could argue that intangible things like entertainment and ambiance are also outputs of a restaurant.
Customers
Customers are the people or organizations that receive your product.
External customers for a restaurant include people who dine in, order delivery or takeout, and even the food delivery service. Internal customers could be the owners or investors of the restaurant.
![]() |
What is the difference between a process map and a SIPOC diagram?
A SIPOC breaks down (high-level) processes into their critical components. It's a summary of a process that doesn't provide many details on the process flow itself.
A high level process map is a more detailed diagram of a process that includes the sequential steps of a process, decisions that impact flow, and where inputs and outputs fit into a process.
The SIPOC diagram is an excellent high-level view of a process.
A process map is helpful for team members working to see precisely where steps fit into a process and what they're dependent on.
Below is an example of a process map showing the process of a requisition moving through an approval process to generate an invoice. The process map uses elements of a SIPOC diagram and shows how they flow together. It starts with the input of a requisition and ends with the output of an invoice. The process map shows the flow (direction) and order of the work.
Creating a SIPOC diagram: an example
Let’s create a SIPOC diagram that shows the elements from the process flow diagram we looked at in the previous section. Below is the SIPOC template we’ll populate in our example.
![]() |
Define the process to diagram
For example, we’ll diagram the process to approve a requisition and generate an invoice. The company in our example is a software development company. Employees submit requests for necessary equipment, such as computer hardware and software programs. The employees who submit requests are from the networking, programming, and QA departments.
Identify suppliers
The suppliers are the employees who create requisitions for our process. Additional suppliers are the managers, VP, and finance department, who provide approvals to keep our requisition moving to become an invoice.
Identify inputs
The inputs are:
- The requisition form.
- The requisition approval system that routes the form for approval.
- The approvals that keep the requisition moving through.
- The invoice generation system that creates the invoice.
Identify the key steps of the process
The key steps of the example processes include creating a requisition, manager approval, VP approval (for purchases over $10,000), finance review, and issuing an invoice.
Identify process outputs
The output is the invoice issued once all the necessary approvals occur.
Identify customers
The customers include the employee submitting the requisition and the approvers: the manager, VP, finance department, and the purchasing department, who’ll pay the invoice so supplies can be purchased.
Create the diagram
Once you identify the components that make up your SIPOC diagram, you’re ready to document it. You can use a spreadsheet tool to create your diagram or access one of the many free SIPOC templates available online. Choosing one standard SIPOC template across your organization is a good idea for consistency.
Here’s what our SIPOC diagram looks like once it is populated.
![]() |
What are the benefits of a SIPOC diagram?
Define new processes
SIPOC diagrams are a starting point for defining a new process. Using the SIPOC, project teams can think about what they need to meet their business goals.
For example, an entrepreneur is starting a new bakery focusing on cakes. Using a SIPOC, the team can brainstorm how to fulfill the cake orders.
The team will need suppliers for the materials they need to make their cakes. Is the bakery starting small, and will it use grocery stores as suppliers? Or do they need to order from suppliers who offer ingredients such as flour in bulk? Is there a farm nearby where the bakery can purchase eggs? Where will they buy equipment?
They'll need to plan their recipes and determine what ingredients are needed. These ingredients are the inputs in the SIPOC diagram. Orders will also be an input. Once the bakers have the necessary supplies, they must decide how to process orders and bake the cake.
The team will also need to determine how they'll accept orders. What type of orders will the bakery take? Phone, internet, app, walk-ins? The answer to this question helps the team determine what other equipment they may need in their bakery (more input on the SIPOC).
The processes for baking a cake would include measuring ingredients, mixing them, baking the cake, and frosting the cake. As procedures are established, the bakers can double-check that they have accounted for all the necessary tools to accomplish this process. They can add any essential supplies they have forgotten to the input list (and make sure they have suppliers for these additional inputs).
The output of the process would be the cake. Yay!
The team should also document their customers. Will the business specialize in birthdays, weddings, or any cake? Documenting the customers can help the team focus their marketing efforts. For example, they could advertise at bridal shows if they want to make wedding cakes. If they plan to target birthday cakes, they could advertise at places children (or, better yet, the parents) go, such as libraries or schools.
Documenting these details in a SIPOC helps make sure the entire team is on the same page (at all times).
Another benefit of documenting these items is that if the business decides to expand to other services in the future, it will have the SIPOC for reference.
For example, the bakery may expand to donuts if the cakes go well. They can review the SIPOC for the cake process to see if there are items that they can reuse for donuts - such as suppliers for ingredients.
Analysis to improve existing processes
SIPOCs are useful for process analysis to identify areas to improve a process. For example, if there are supply issues, you can use the SIPOC to discuss other options.
Using DMAIC, once a team defines a process in a SIPOC, the team can measure what supplies the team has run short on and how much. They can analyze current suppliers and brainstorm replacement or additional suppliers. They can then try to improve the process by finding new suppliers (but should check if the changes resolve the issues).
When you keep processes running smoothly or (better yet) improve them, customer satisfaction tends to improve. Happy customers mean increased profits.
Transparency
For transparency, the SIPOC is a great way to convey to the teams and relevant stakeholders what's involved in a process.
For example, if a purchasing department uses the invoice produced by your approval process, a SIPOC diagram can help them see who is involved in your approval process. They know who to ask if they have a question about the approval.
New employee training
New employees can use the documentation as a reference for training purposes.
Your employees can learn where the supplies they use come from, what's needed to complete the process, and who the target customers are. They'll get a high-level understanding of the whole process, not just their part.
![]() |
Use Motion to improve business processes
Once you've created a SIPOC diagram to understand your processes, consider using Motion's calendar feature to schedule essential tasks that need to be completed to keep things moving.
For example, if you recently added new suppliers because of supply issues, add a task to your calendar to track the new supplier. When you specify a priority and deadline on a task, Motion will ensure the task is scheduled before the deadline and alert you if the task is in danger of missing a deadline so you can adjust your schedule.
If you aren't already using Motion, access a free trial today.
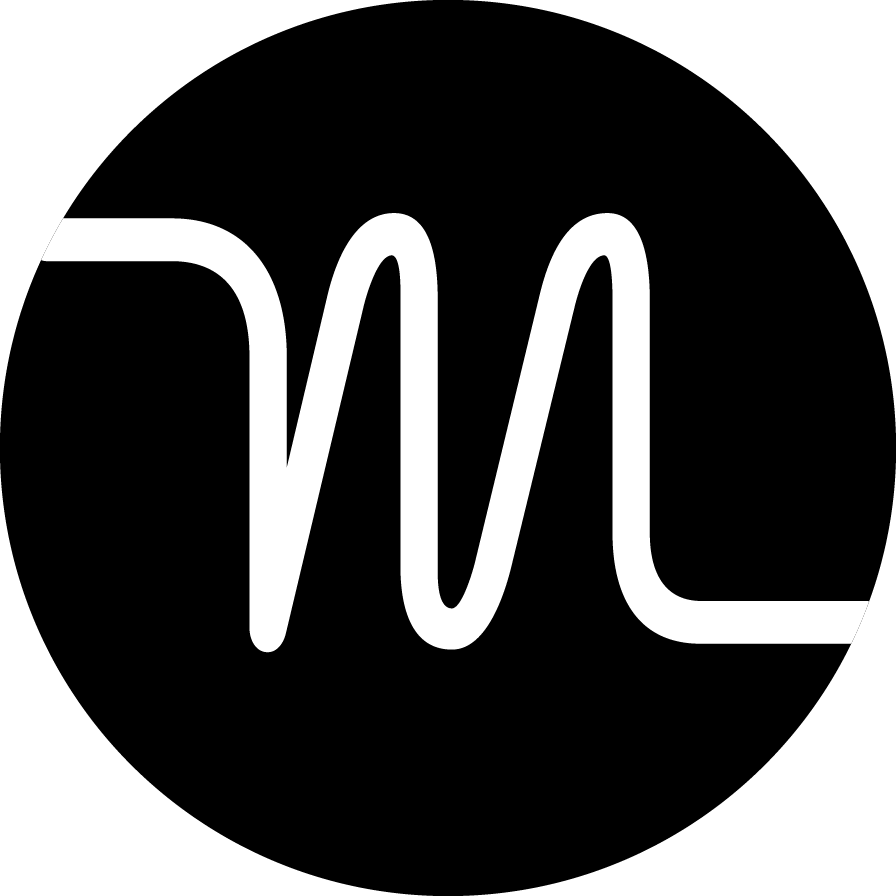