It may seem difficult to argue against improving business processes for better performance in the factory and on the books. Still, many business owners and managers don't see the need. Often, the attitude is: "We've been doing what we do, the way we do it, for a very long time, and we just don't see a reason to change anything."
What they're missing is that change is all around us, whether we like it or not. Markets change, customers change, products change, and many other things. We must respond to these changes, or our business will get left behind.
This is where business process management can help.
Business process management can reduce manufacturing time, streamline value delivery, get products to market faster, and improve our productivity.
Choosing the right path
Once you've decided that current processes need improving, you may need help choosing the best tools and business process improvement methodology. And this is not surprising because even the names of these systems can create confusion.
Kaizen, Kanban, 5S, PDCA, Six Sigma, cause and effect analysis, SIPOC analysis, value stream mapping (VSM), total quality management (TQM), and process mapping are all possible methodologies. So which is the right choice?
To answer that, we need to dig into each one a little, but it helps to understand that most are designed as tools for continuous process improvement. And, since process mapping is a part of every process improvement discipline, it makes sense to begin there.
The methodologies
Process mapping
Often associated with Six Sigma, process mapping is actually a distinct tool and discipline. The purpose of the exercise is to document and communicate how a given process works unambiguously. As a result, process mapping has become an essential part of almost every process improvement methodology.
![]() |
Even without embarking on a full process improvement project, organizations often need to map their current processes. They typically do this to share how things are done and see where improvements can be made.
One of the best-known ways to build a map of your current process is by using Business Process Modeling and Notation (BPMN). Many online BPMN tools provide a set of flowchart symbols and the means to place and connect these on a process map.
Tools for more complex processes dealing with multiple objects are based on another notation mechanism: Unified Modeling Language (UML). This allows more detail to be captured in different views.
Kanban
Expressed in simple terms, Kanban is a work management system designed to help visualize work and restrict the amount of work-in-progress while also maximizing flow or efficiency. The system is designed to help teams visualize their workflow and prioritize tasks.
![]() |
It can be a useful tool for project management, and you can use Motion's Intelligent Calendar to dip your toes in the Kanban water. The visual representation of a project's progress helps teams manage their workflow and prioritize tasks.
It facilitates excellent team organization and allows team members to prioritize tasks, working together more effectively. It also enables you to track the overall progress of the project.
Some advantages of Kanban are that it's easy to use, is useful in many different settings, is customizable, and helps teams to collaborate. But it does have a couple of areas for improvement. Kanban boards do not usually reflect project timelines, and the methodology can struggle in more dynamic project environments.
Kaizen
Like Kanban, kaizen originated in Japan and garnered global attention when Toyota used it to improve its vehicle manufacturing quality. What was unique is that it did so through incremental and continuous improvements by workers on the factory floor.
![]() |
Among the more interesting elements of kaizen is when managers “Go to Gemba,” which refers to the factory floor or anywhere a product is produced. Gemba also doesn’t have to be a physical location; it can be a virtual space within which a team works.
Either way, the principle remains the same: Managers visit the front line where work is done to interact and observe the process in action. Pros of using kaizen include improved safety, teamwork, efficiency, and greater employee satisfaction. Kaizen also helps to build leadership skills.
The cons are few, but they can be show-stoppers. Kaizen requires a change in approach from everybody, and change is difficult, can cause friction, and needs persistence to bed it down.
5S
Although the original five words also begin with an S, an English translation was needed when kaizen began gaining global traction. This translation became: sort, set in order (or straighten), shine, standardize, and sustain.
The principle is to create a clean, uncluttered, safe, and well-organized workplace. This enables a reduction in waste and improved productivity. The idea is that a quality work environment will physically and mentally benefit employees and visiting customers.
PDCA
Also called the Deming Cycle, PDCA is an acronym for a continuous improvement model based on a logical sequence of four repetitive steps: Plan, Do, Check (or Study), and Act. It is the core principle of kaizen.
The first step is to plan for change. The second one is to implement that plan. The third is to check or measure the new processes and compare the results against the expected results. And the final step is to act on that information. PDCA should be a never-ending iteration.
Six Sigma
Six Sigma is a data-driven methodology offering the tools and techniques needed to define and measure every process step. It also provides ways to increase efficiency, improve quality, and positively affect the bottom line.
Like kaizen, it initially found traction in manufacturing but has since been employed by businesses in various industries. The main advantage of Six Sigma is that its quality control is customer-driven rather than internal. Also, because it addresses the entire process behind creating a product or service, it is proactive rather than reactive.
However, since the process improvement methodology is applied to all aspects of production and planning, it may create rigidity and bureaucracy, causing delays and stifling creativity. This disadvantage means that Six Sigma can also become very expensive.
SIPOC analysis
Among the tools suggested in the Six Sigma methodology is SIPOC, an acronym for Suppliers, Inputs, Process, Outputs, and Customers. Where the rubber meets the road, it is a process mapping and improvement framework that summarizes process inputs and outputs in a single diagram.
In that way, it’s much like process mapping, and it also helps the project team to identify all the opportunities for improvement before work begins.
Cause and effect analysis
Another way to improve processes is to single out a particular known problem and to work to establish the causes of that problem. In this way, removing or addressing the cause of dysfunction can improve the processes.
This is where cause and effect analysis is useful. It's a technique that can help you identify all the factors that could create the problem. And a central element to enable the analysis is what's known as a fishbone diagram.
![]() |
The approach's pros include that it allows for thoughtful analysis, is easy to implement, and results in an easy-to-understand visual representation. This enables the team to focus on the "big picture”.
The main con of this approach is that a fishbone diagram can make it difficult to fully reflect the interrelated nature of causes and effects within complex environments.
Value stream mapping
Like Kanban and kaizen, Toyota highlighted the benefits of using value stream mapping (VSM) to document every process step in a flowchart. Engineers at the Japanese company created the original VSM template.
It has since become a critical tool in lean project management, and many practitioners use it to identify wastage, cut the cycle times of processes, and support process improvement projects. It helps users create robust implementation plans that will maximize the available resources and ensure that materials and time are used efficiently.
Business process management
Business process management (BPM) is a popular methodology for process improvement. Like Six Sigma, it has five phases: Design, Model, Implement, Monitor and Optimize.
The objective of BPM is to model and analyze each process targeted for improvement, and design an improved proces. The improved process is piloted, measured against performance indicators, then optimized and deployed.
BPM is not “once and done”, though. When done right, it creates a culture of continuous improvement. Companies that adopt it understand that their processes are the lifeblood of their growth and success. They adopt BPM as an integral way of working to increase efficiency, improve response times, and optimize value received and given.
Total quality management
The Oxford Dictionary defines total quality management (TQM) as “a system of management based on the principle that every member of staff must be committed to maintaining high standards of work in every aspect of a company's operations.”
In practice, it is a continual process to detect and reduce or eliminate errors in manufacturing. But it can also help to streamline supply chain management, improve customer satisfaction, and ensure that employees are up to speed with training.
As suggested by the Dons of Oxford, it aims to hold all parties involved in the process accountable for the quality of the end product or service.
Which should you choose?
Well, that’s complicated. You could probably use any or all of these methodologies and tools for continuous process improvement in your business. All of them are applicable across multiple industries, and each has an army of practitioners ready to consult and show you the way.
But if you don't have an appetite for large consulting fees, you should take advantage of Motion's 7-day free trial to explore its Intelligent Calendar. This product incorporates Kanban for task assignment and prioritization, allowing you to experiment with a Kanban board. It's an ideal way to wet your feet in the world of process improvement and increase your and your team's productivity.
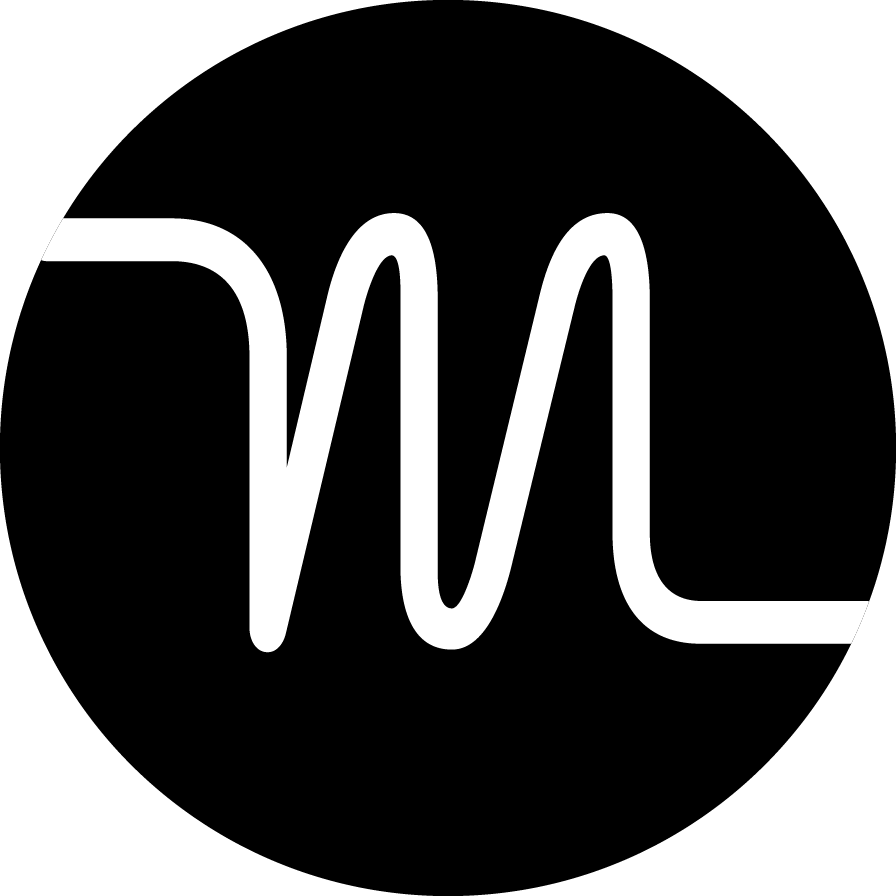